Argovia Projects 2018
The following projects started in 2018.
PROJECT | PROJECT LEADER | COLLABORATORS | |
---|---|---|---|
13.01 NANOCREATE– NANOCatalyst etching and laser machining for grating interferometry based breast ct sysem | Dr. Konstantins Jefimovs (PSI) | Dr. Lucia Romano (PSI & ETHZ) Prof. Dr. Ronald Holtz (FHNW Windisch) Dr. Bojan Resan (FHNW Windisch) Dr. Martin Stauber (GratXray AG, Villigen) Dr. Zhentian Wang (GratXray AG, Villigen) | |
13.04 ecamist – Efficient capturing of mRNA for single-cell transcriptomics | Prof. Dr. Georg Lipps (FHNW Muttenz) | Dr. Martin Held (ETHZ Basel, D-BSSE) Dr. Simone Schmitt (Memo Therapeutics AG, Basel) | |
13.08 MEGAnanoPower – Disruptive power storage technology applying electrolyte nano dispersions and micro/ nano structured electrodes | Prof. Dr. Uwe Pieles (FHNW Muttenz) | Dr. Sören Fricke (CSEM Muttenz) Andreas Schimanski (Aigys AG, Rheinfelden) | |
13.09 NanoCoat – Biomimetic growth of calcium phosphates ceramics on Ti implants | Dr. Andrea Testino (PSI) | Dr. Elisabeth Müller (PSI) Prof. Dr. Michael de Wild (FNHW Muttenz) Philipp Gruner (Medicoat AG, Mägenwil) Dr. Jan Moens (Medicoat AG, Mägenwil) Dr. Walter Moser (Atesos Medical AG, Aarau) Dr.-Ing. Burkhard Höchst (Hager & Meisinger GmbH, Neuss) | |
13.12 NanoGhip – Nano-switchable GPCR–arrestin biochip for drug discovery | Dr. Martin K. Ostermaier (InterAx Biotech AG, Villigen) | Prof. Gebhard F.X. Schertler (PSI) Prof. Dr. Cornelia Palivan (Dept. of Chemistry, University of Basel) Prof. Dr. Roderick Y.H. Lim (Biozentrum, University of Basel) | |
13.13 NanoTough – Self-assembled block copolymers for nanoscale toughening of structural composite materials | Prof. Dr. Clemens Dransfeld (FHNW Windisch) | Prof. Dr. Wolfgang Meier (Dept. of Chemistry, University of Basel) Dr. Alessandro Napoli (Huntsman, Basel) | |
13.15 NQsense – Nanophotonics for quantum sensing technology | Prof. Dr. Patrick Maletinsky (Dept. of Physics, University of Basel) | Dr. Christian David (PSI) Dr. Gediminas Seniutinas (PSI) Dr. Felipe Favaro (Dept. of Physics, University of Basel & QNAMI) Dr. Mathieu Munsch (QNAMI) |
13.01 NANOCREATE - Using gratings to boost contrast – The Nano Argovia project “NANOCREATE” aids the optimization of diagnostic images
In the Nano-Argovia project “NANOCREATE”, scientists from the Paul Scherrer Institute (PSI), in collaboration with the University of Applied Sciences (FHNW) and GratXray AG (Villigen, AG), are developing a cost-effective fabrication method for optical X-ray gratings. These gratings are used in a computed tomography (CT) scanner developed by GratXray that allows for high-resolution, high-contrast imaging of low absorbing tissues, such as the female breast.
Decisive advantages
In classic X-ray imaging, contrast between different tissue types get better the lower the X-ray energy. However, the lower the X-ray energy, the higher the radiation dose that is deposited in the patient. Therefore, classical X-ray imaging is physically limited by the image contrast that can be reached. This limitation can partially be overcome with grating interferometry, where not only the absorption, but also the refraction and scatter of X-ray can be measured. These additional signals are much stronger in soft tissue and thus, allow to significantly improve image contrast under dose control. Integrated in a dedicated breast CT, this technique allows for retrieving unprecedented image quality in 3D, ultimately leading to a more accurate diagnosis of breast cancer.
New fabrication method
Grating interferometry for medical diagnostics has been developed extensively in recent years, but the high production costs of specialized gratings remains a limiting factor for the technique’s broad application. The team behind the Nano Argovia project “NANOCREATE”, led by Dr. Konstantins Jefimovs (PSI), is therefore focusing on the development of alternative manufacturing method, to lower fabrication cost so that gratings can be produced on larger area and in higher volumes.
The scientists at PSI are developing a method based on metal assisted chemical etching to produce silicon structures of high aspect ratio, larger area and lower costs. These structures, which have low X-ray absorbance, are then filled with gold, strongly absorbing X-ray. They want to produce and test the grating performance manufactured by this new method on a lab CT-system. On the other hand, the team at FHNW is testing laser ablation as an alternative method to directly make the gratings from a metal foil. These techniques are now being examined in greater detail as part of the Nano Argovia project.
In addition to the project leader, Dr. Konstantins Jefimovs (PSI), the team consists of Professor Lucia Romano (PSI), Professor Ronald Holtz (FHNW), Dr. Bojan Resan (FHNW), as well as Dr. Martin Stauber and Dr. Zhentian Wang (both of GratXray AG). “The Nano Argovia project “NANOCREATE” will help us in our efforts to make grating interferometry available for a broad range of applications,” says Dr. Martin Stauber of GratXray, a spin-off company of PSI.
13.04 ecamist - Messenger RNA in the crosshairs – The Nano Argovia project “ecamist” aims to improve single-cell analysis
The aim of the Nano Argovia project “ecamist” is to develop an effective method for working up messenger RNA from single cells. A team of scientists from the School of Life Sciences at the University of Applied Sciences Northwestern Switzerland (FHNW), the Department of Biosystems Science and Engineering at the Federal Institute of Technology (ETH) Zurich in Basel (D-BSSE), and the company Memo Therapeutics AG (Basel) wants to improve the yield and quality of isolated messenger RNA compared with existing methods. Among other applications, the information about the messenger RNA present in a cell can be used to derive conclusions about the development of diseases. It is also important for studying cell lines used in antibody production, for example.
Analysis of individual cells
Nowadays, messenger RNA (mRNA) is often analyzed to determine which genes are active in cells. Inside a cell, the mRNA acts as a mediator between the hereditary information stored in the DNA and the ribosomal RNA, which is needed for protein synthesis in cell ribosomes. When examining various research questions, scientists now increasingly opt to analyze the mRNA in single cells instead of analyzing mixtures of an entire cell culture. Single-cell analysis is particularly useful for understanding the development of diseases, as defective processes often begin in individual cells
Bound to small beads
Nowadays, messenger RNA (mRNA) is often analyzed to determine which genes are active in cells. Inside a cell, the mRNA acts as a mediator between the hereditary information stored in the DNA and the ribosomal RNA, which is needed for protein synthesis in cell ribosomes. When examining various research questions, scientists now increasingly opt to analyze the mRNA in single cells instead of analyzing mixtures of an entire cell culture. Single-cell analysis is particularly useful for understanding the development of diseases, as defective processes often begin in individual cells
Enzyme selection is crucial
The researchers led by Professor Georg Lipps and Dr. Martin Held from the Department of Biosystems Science and Engineering (D-BSSE) therefore want to immobilize the hybridized mRNA segments by establishing a covalent, more thermally stable bond to the microbeads’ surface. They hope that this will lead to a greater yield of bound mRNA on the microbeads, as well as fewer impurities and therefore a higher-quality mRNA yield. The project hinges on selecting a suitable enzyme that catalyzes the formation of covalent bonds to the microbeads and that works reliably even in high salt and detergent concentrations, as these conditions are necessary for lysing the cells.
“For Memo Therapeutics, the Nano Argovia project is a good opportunity to extend single-cell analytics with additional protocols and hence to further expand our activities in the area of antibody development,” says Dr. Simone Schmitt, Senior Scientist at Memo Therapeutics and an industrial partner within the Nano Argovia project “ecamist”.
13.08 MEGAnanoPower - Nanoparticles for mega power – The “MEGAnanoPower” project aims to optimize an innovative energy storage device
In the Nano Argovia project “MEGAnanoPower”, scientists from the FHNW School of Life Sciences, the CSEM in Muttenz, and the industrial partner Aigys AG (Othmarsingen, AG) are seeking to optimize the PowerCell® battery, which was invented by Aigys. Using environmentally friendly materials, the researchers hope to develop a sustainable and affordable energy storage device for large-scale applications.
New storage media needed
Renewable energies such as wind and solar power are becoming an increasingly important part of our energy supply. As these energy sources continue to expand, there is a need for new storage media that can not only absorb peaks in energy production but also make energy available quickly in the event of prolonged periods of time without wind or sunshine.
Until now, research into storage media has centered around lithium-ion batteries. Instead, the “MEGAnanoPower” project is focusing its attention on a flow cell battery in order to avoid the key disadvantages that lithium-ion batteries exhibit. Since it was founded in 2011, the company Aigys AG has been actively involved in the search for alternatives and has patented a special flow cell battery known as the PowerCell®. The project partners, Professor Uwe Pieles from the School of Life Sciences at the University of Applied Sciences Northwestern Switzerland (FHNW), Dr. Sören Fricke from the CSEM (Centre Suisse d’Electronique et de Microtechnique) in Muttenz, and Dipl.-Ing. Andreas Schimanski, CEO of Aigys, are studying various approaches to further optimize the battery.
Energy supplied by an electrochemical reaction
As in a conventional flow cell battery, the PowerCell® stores electrical energy in the form of chemical compounds, which are held in two separate circuits. One circuit contains ions that have a high electronegativity and therefore readily accept electrons (e.g. Zn2+). A second, separate circuit contains ions with a lower electronegativity, which readily donate electrons (e.g. Cer3+). Ions are exchanged between the two circuits across a membrane, resulting in electron donation on one side of the membrane and electron acceptance on the other side. These oxidation and reduction processes release electrical energy. Unlike in a conventional flow cell battery, however, the charge carriers in the PowerCell® are not held in solution. Instead, high-pressure technology is used to disperse them into the electrolytes in the form of small spheres measuring just a few micrometers in diameter.
MEGAnanoPower to increase storage capacity
These small particles in the dispersion need to be stabilized over a prolonged period of time and a higher charge density needs to be achieved. “We want to reduce the particle size of the solid electrolytes in order to achieve a higher energy density,” says Aigys CEO Andreas Schimanski on the project’s objectives. “In order to exploit the full potential of our PowerCell®, we’re relying on the expertise of the interdisciplinary team behind the Nano Argovia project MEGAnanoPower.” The overall aim is to increase the solid electrolyte content in order to expand the storage capacity. In addition, the researchers are studying how the electrodes can be improved and how the membrane must be adapted to nanoparticles with a view to improving the efficiency of the electrochemical reaction. In all modifications, the interdisciplinary team is taking care to use abundant, environmentally friendly materials and compounds that solve the energy storage problem in a genuinely sustainable manner without causing problems in industrial operations.
13.09 NanoCoat - Ceramic coating of bone implants – A cost-effective process is being developed in the “NanoCoat” Nano Argovia project
An interdisciplinary team at the Paul Scherrer Institute (PSI) and the University of Applied Sciences Northwestern Switzerland (FHNW) is working with three industry partners on the Nano Argovia program. The researchers are developing a protocol for coating titanium implants with calcium phosphates ceramics, which will improve the integration of implants into new bone growth, and therefore ensure a better stability of the implant.
Integration in the bones essential
Thanks to new technologies, increased prosperity, and an ever-ageing population, the demand for bone implants is continually growing. Implants are primarily comprised of metallic materials; titanium is particularly popular due to its excellent mechanical properties and its optimal biological compatibility, and is often used in dentistry, plastic surgery and orthopedics. In order to guarantee the long-term integration of a titanium implant into the bone, bone-building cells (osteoblasts) must be able to settle on the implant’s surface. They form new bone cells and the implant is then gradually incorporated into the existing bone. In the past, different methods were developed to encourage the forming of bone cells on the implant surface as well as the implant’s incorporation into the bone. Coating with hydroxyapatite has proven to be a promising method. Hydroxyapatite is a calcium phosphate compound and a main constituent of bone. In the market of orthopedic implants, plasma spray has been established as coating process.
An energy-saving method is being developed
In the “NanoCoat” Nano Argovia Project, a team of scientists under the lead of Dr. Andrea Testino from the Paul Scherrer Institute is now investigating a more cost- and energy-efficient method for coating titanium surfaces with calcium phosphate. Alongside Dr. Andrea Testino, the team comprises Dr. Elisabeth Müller (PSI), Professor Michael de Wild (FHNW) as well as Philipp Gruner (Medicoat AG, Mägenwil, Aarau), Dr. Burkard Höchst (Hager & Meisinger GmbH, Neuss, Deutschland) and Dr. Walter Moser (Atesos Medical AG, Aarau).
In the first phase of the project, the researchers are using a chemical and thermal treatment to transform the smooth titanium surface of the implant into a raw and porous one. In the subsequent coating stage, the implant is placed into a coating reactor where a special solution, containing the calcium phosphate precursors, was poured. The researchers were able to prove that, under controlled conditions, the calcium phosphate phase grows both onto the implant and inside a porous layer, ensuring an optimal grafting of the thin calcium phosphate phase on titanium. As a results, the titanium implant is already coated with a synthetic bone.
“In the Nano Argovia project, we are optimistic that we will develop a new cost-efficient, alternative method for coating of implants which support integration into natural bone material. We hope to open new market fields that our plasma spray technique cannot access” says Philipp Gruner, one of the “NanoCoat” project’s three industry partners.
13.12 NanoGhip - Detecting tiny changes using biosensors – The Nano Argovia project NanoGhip is developing a prototype of a biochip for drug discovery
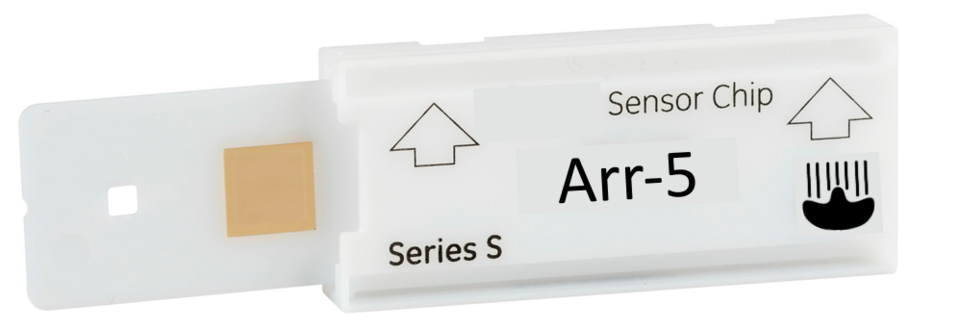
On a chip measuring approximately 10 x 10 mm (gold square), tiny artificial vesicles with integrated protein complexes are placed in four small channels (volume: 0.06 µl). Then, biosensors are used to observe how various test substances affect the protein complexes. The data provides information about the biological properties of the test substances, ultimately allowing researchers to draw conclusions regarding the efficacy and safety of the potential active pharmaceutical ingredients they are studying (Image: InterAx Biotech/Biozentrum).
In the Nano Argovia project NanoGhip, an interdisciplinary team led by Dr. Martin Ostermaier from InterAx Biotech AG (Villigen, AG) is investigating a new screening method for active substances that could lead to the discovery of new medicines. The scientists aim to develop a new type of biochip that analyzes how the chemical and biological molecules in question react with protein complexes in real time. Even at this early stage, it could also provide information about the safety profile of the tested compounds.
Relaying signals
Membrane proteins play an important role in our cells. As well as being fundamental for our survival, they are involved in the development and treatment of diseases. In this context, G protein–coupled (GCP) receptors are particularly significant. Among other functions, they relay signals to the cell’s interior and thereby regulate a whole cascade of vital reactions. In doing so, many of these G protein–coupled receptors interact with a wide range of proteins to form protein complexes.
Searching for new active substances that influence these receptors is difficult because, instead of analyzing one individual protein, it is important to consider entire protein complexes in order to replicate the natural conditions in the cell as closely as possible. Given that these protein complexes are anchored within membranes in their natural environment, they must also be integrated into membranes for the screening process.
Tiny changes
In order to create a biochip, the researchers in the NanoGhip project incorporate natural protein complexes into synthetic membranes. These have very similar properties to the natural membranes but surpass their natural counterparts in terms of robustness. The researchers then use biosensors to monitor structural changes in the protein complexes when test substances come into contact with the system. These tiny conformational changes of the G protein–coupled receptors have a magnitude of just 0.1 to 1.4 nanometers. Using the protein-based biosensors, the scientists derive information about whether a test substance prevents the GPC receptors from relaying signals to the cell’s interior.
The Nano Argovia project NanoGhip is a close collaboration by scientists from InterAx (a start-up of the Paul Scherrer Institute and ETH Zurich), the Paul Scherrer Institute, and the Department of Chemistry and Biozentrum at the University of Basel, with each of them contributing their own very different areas of expertise. “In this project, we’ve brought together a unique combination of experts that allows us to exploit synergies and explore a new approach to the biological screening of substances on a chip,” summarizes project leader Martin Ostermaier.
13.13 NanoTough - Lightweight and stable – The Nano Argovia project “NanoTough” is investigating new methods for improving the toughness of composite materials
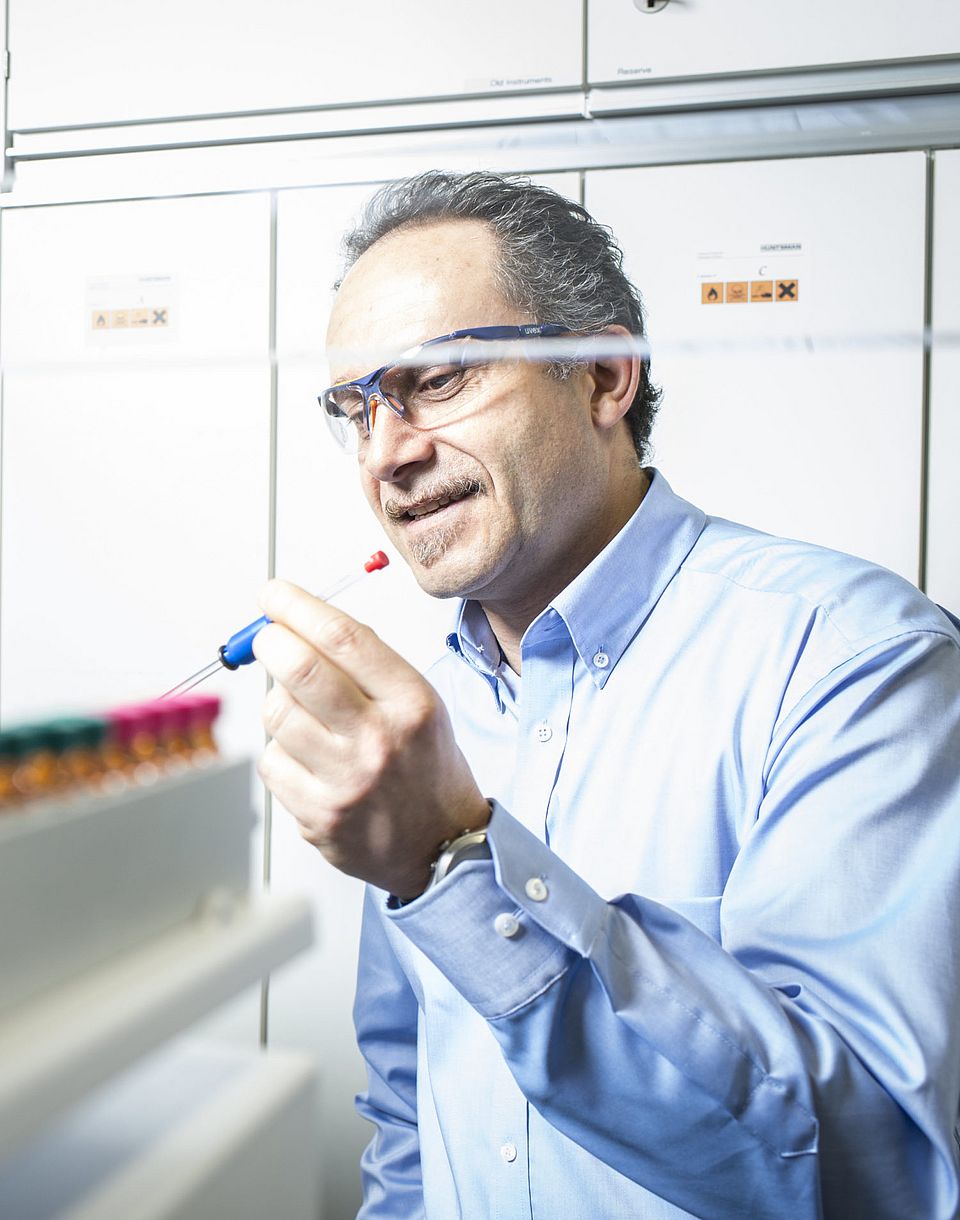
“By participating in the Nano Argovia project “Nano-Tough”, we are expanding our knowledge of new composite materials and hope to further consolidate our leading position in this area,” says Dr. Alessandro Napoli, Global Technology Manager at Huntsman, speaking about the company’s involvement in the project. (Image: Huntsman Advanced Materials GmbH)
In the Nano Argovia project “NanoTough”, scientists from the University of Applied Sciences and Arts Northwestern Switzerland (FHNW), the University of Basel, and the company Huntsman Advanced Materials GmbH (Basel) are investigating the use of block copolymers in composite materials. The aim is to make composites tougher without impairing their workability.
Room for improvement
Plastics that have been reinforced with carbon fibers (fiber-reinforced composites) stand out for their combination of extraordinary mechanical properties and low weight. They are primarily used for building vehicles, aircraft, and ships but also play an increasingly important role in the manufacturing of wind turbines. Their range of applications could be expanded further if the materials were less brittle and if their toughness could be improved. This can already be achieved today by adding thermoplastic powders, but the use of such additives increases the materials’ viscosity and therefore makes them harder to work.
Block copolymers as an additive
The teams of scientists working on the Nano Argovia project “NanoTough” begin by investigating the synthesis of various block copolymers, which they later add to an epoxy resin that acts as a matrix. Block copolymers are polymers assembled from at least two different monomers, with single molecules of the monomers linking up in long chains to form the individual blocks (e.g. AAAAABBBBB). The group led by Professor Wolfgang Meier from the Department of Chemistry first synthesizes a variety of block copolymers (BCPs) with different compositions and masses and then studies how these affect the morphology of the resulting nanostructures.
In addition, the researchers attempt to simulate the conditions found in an epoxy resin system by selecting different solvents and temperatures. Once the BCPs are synthesized and characterized, suitable candidates are selected and then tested in an epoxy resin system by the team working under project leader Dr. Sonja Neuhaus and Professor Clemens Dransfeld (FHNW School of Engineering, Windisch). Key factors include not only the conditions during curing but also the morphology of the block copolymers in fully cured samples. A thermoplastic material is then added, and the morphological characteristics of the new composite material are analyzed.
Lastly, partner company Huntsman works with the FHNW team to characterize the samples’ mechanical properties and compare them with leading commercially available materials. This work centers around experiments to test the fracture properties and the determination of the glass transition temperature under a variety of conditions.
13.15 NQsense - Working together to improve light yield – The Nano Argovia project NQsense seeks to optimize the sensitivity of quantum sensors for nanoscale applications
In the NQsense project, the team working under project leader Professor Patrick Maletinsky plans to fabricate a fully integrated quantum sensor with significantly improved sensitivity. This sensor could be used, for example, to support basic scientific research in the areas of materials science or to perform failure analyses in the semiconductor industry.
Diamonds as sensors
The team of scientists from the Department of Physics at the University of Basel, the Paul Scherrer Institute, and the industrial partner Qnami – a start-up from the Department of Physics at the University of Basel – is basing its work on tiny quantum sensors made of diamonds.
These are created by deliberately removing two carbon atoms from the diamonds’ crystal lattice. One is replaced with a nitrogen atom, and the second is left as a vacant site in the lattice. These nitrogen-vacancy centers (NV centers) host individual electrons that can be excited and manipulated. The intrinsic angular momentum (spin) of these electrons, and their electric dipole, are extremely sensitive to tiny magnetic and electric fields. Exposing the diamond sensor to fields of this kind causes a change in the intensity of the NV center’s luminescence. This can be detected using an optical device and used to draw specific conclusions about the influencing field.
Ambitious goals
In recent years, the team has already achieved significant improvements in the tiny sensors’ complex and demanding production process. Now, the scientists are exploring ways to boost the sensitivity of their sensors. That is easier said than done, because diamonds have a high refractive index. As a result, most of the light emitted by the NV centers is reflected inwards by the outer surfaces, leaving it unavailable for measurements.
“At the moment, we can use about one to two percent of the emitted photons for our measurements. As part of the Nano Argovia project NQsense, we now want to design and produce structures that allow us to boost the yield to up to 50 percent,” comments Professor Patrick Maletinsky on the impending challenge.
“The Nano Argovia program offers the ideal framework for our product’s further development, as we can exploit synergies with our partners at the University of Basel and the Paul Scherrer Institute, as well as benefiting from our partners’ excellent technical equipment,” says Mathieu Munsch, CEO of the industrial partner, Qnami.